Innovative social enterprises are recycling biowaste into affordable carbon-neutral biomass fuels in Kenya
Amid a monotonous din, Elizabeth Nyamai feeds cubes of peeled and washed tubers into an electric grater. Not even the noise from the grater dampens her determination to process the starch slurry that is dried and sold to food processing companies and other users.
Nyamai is the director of Veliz Foods, a food processing enterprise based in Machakos County, some 60 km from Kenya’s capital, Nairobi. Her firm supplies several food manufacturing companies with dried and semi-processed food products for making flour and blending with various food products. Crops processed include cassava, sweet potatoes, pumpkin and African leafy vegetables sourced from farmers in the region.
However, of particular interest is how Veliz dries its food; the firm uses technology from BioAfriq Energy Limited, a Kenyan social enterprise that recycles bio-waste, sourced from thousands of farmers in south-eastern Kenya, into affordable carbon-neutral biomass fuels.
Nyamai notes that she has lowered her production costs using BioAfriq’s briquettes and a drier bought from the enterprise. “My expenditure on electricity is low, yet I am able to dry my products in large quantities without undermining their quality,” she says.
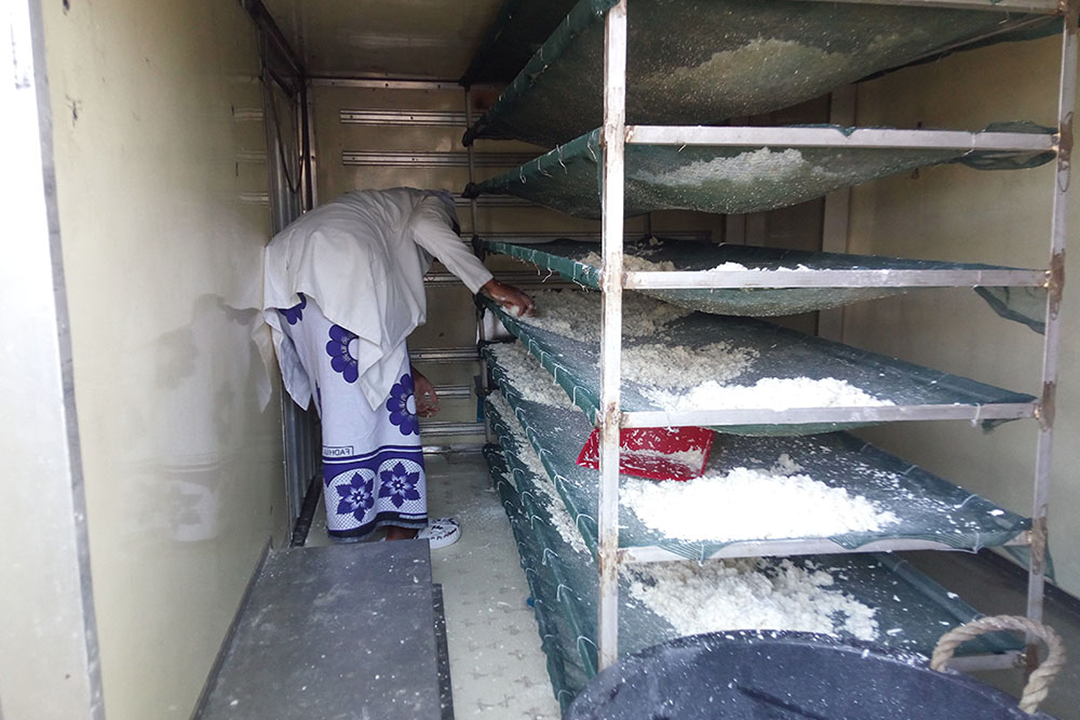
Elizabeth Nymai, director of Veliz Foods checks stock at her food processing plant. Photo: Justus Wanzala
James Ivisu, a founder of BioAfriq, says the biomass fuel is made crop waste that are thrown away. “We recycle them,” he says. The briquettes are sold to farmers who have bought driers, as well as to other users, as a substitute for charcoal, firewood or liquefied petroleum gas.
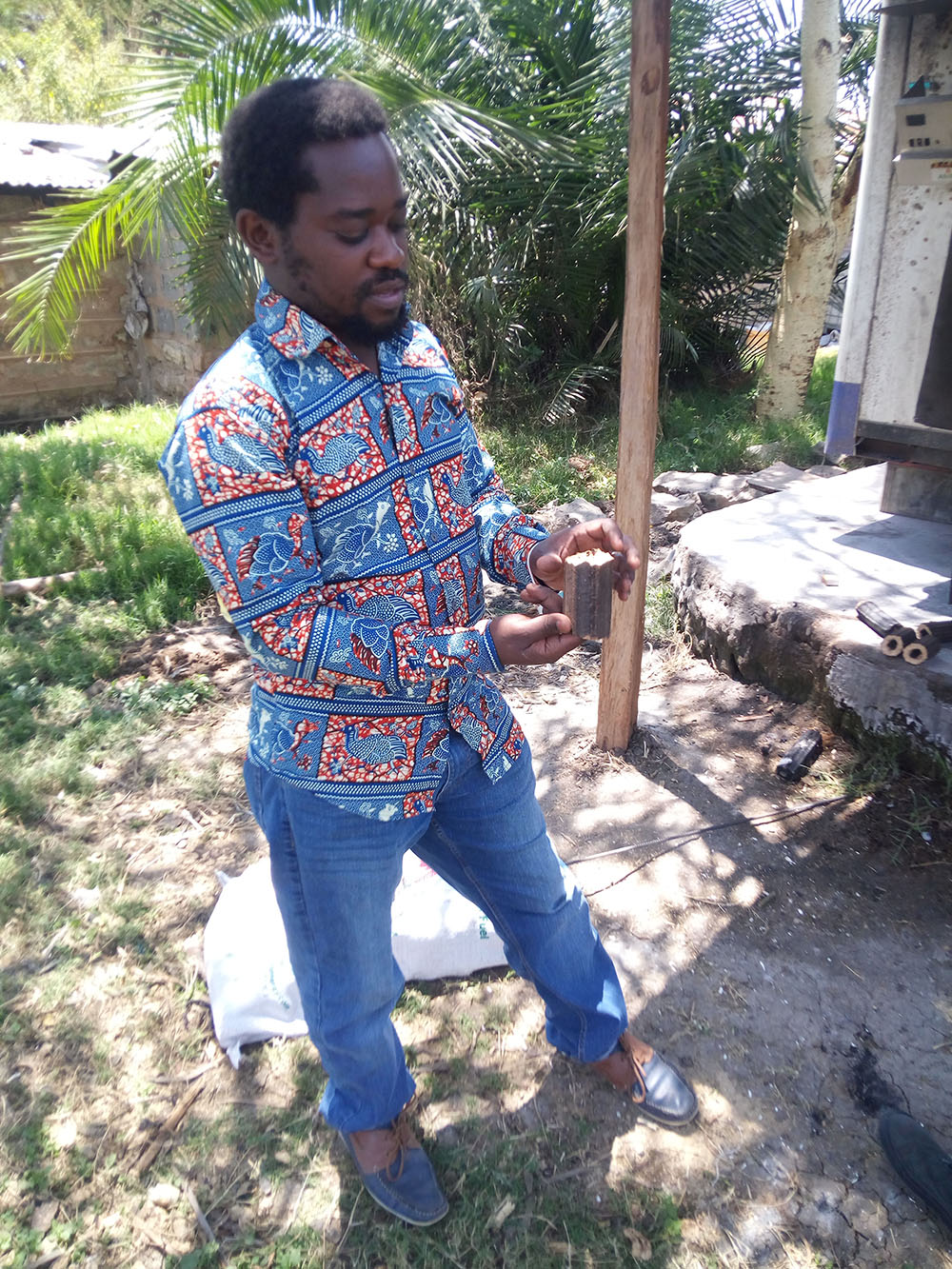
James Ivisu, the director of Bioafriq Limited, holding an example of the briquettes his company makes. Photo Justus Wanzala
BioAfriq co-founder Dorine Achieng describes their focus as developing solutions for properly preserving produce, adding value and providing clean energy to households and light industry. Ivisu further explains that farmers in the area have in the past relied on the sun for drying produce, leaving them vulnerable to unpredictable weather patterns.
“It is a challenge to dry produce throughout the year,” he told Africa in Fact. “Farmers lose harvest that could actually be salvaged. It is estimated that Kenya loses produce worth 150 billion Kenya Shillings annually ($150m).” But, he adds, about 65% of what is lost could be salvaged through improved drying techniques.
Ivisu says farmers had resorted to buying ordinary solar driers to preserve their farm produce, but these were unreliable, with drying taking longer and the produce becoming prone to bacteria infestation, which meant a loss of nutrients. The produce processed with ordinary solar driers also absorbed moisture at night, and drying had to be redone. “It is like defrosting and freezing meat for days on end, which inevitably affects its quality,” he says. “Our innovation offers solutions that can dry food faster and evenly, reducing losses even when there is no sunlight.”
Ivisu, who initially ventured into chicken keeping, says the high cost of charcoal he used to warm the chicken compelled him to explore viable and affordable alternatives. “I was buying 30 bags in a month at a cost that was depleting my profits,” he says. Furthermore, the place he was sourcing the charcoal from was fast losing its tree cover. “It pained me to realise that I was aiding in the destruction of the forest and I had to seek a solution.”
BioAfriq Energy Limited’s venture resonates with other African bio-energy enterprises that support similar initiatives. Kobus Venter, the chief executive officer of Vuthisa Technologies, a South African company that offers green technology solutions, says while southern African countries have been rather slow to take up biotechnical products, his company has partnered with the United States-based Legacy Foundation to provide training and technology services for biomass fuel briquette production. Communities in 11 countries have already benefited from the technology, Venter says.
The technologies promoted use both biomass and agricultural waste made from agricultural as well as commercial residues such as weeds and carton boards.
Referring to the ever-growing problems of poverty and deforestation caused by the widespread use of firewood and charcoal as energy in the absence of an affordable alternative, Venter says the small network of briquette makers at present does not have the capacity to provide for the level of demand. He points out that entrepreneurs lack access to information and better marketing skills. “They need support for marketing products, branding and processing,” he notes. They also require information on assessment of thermal capacity, emissions and standards.
Godfrey Sanga, the East Africa regional director for Energy 4 Impact, a non-profit organisation working with local businesses in East and West Africa to grow sustainable, clean energy markets, agrees that the use of briquettes in sub-Saharan Africa is still limited. “Poultry farmers do use them, but household use is smaller,” he says. Sanga points out that competing use of the materials used, for instance in animal feeds, limits availability of stock. “Lack of appropriate briquetting technology is another limitation,” he says.
The cost of purchasing and importing, operating and maintaining briquette-making machines, tax and duties are also a barrier to expanding production. There are other challenges to expanding the market and encouraging demand: long distances between producers and consumers mean high transportation costs, for example.
Sanga does, however, believe there is scope to expand and upscale briquette manufacturing, suggesting linkages between potential agro-waste briquette manufacturers and potential buyers to enhance the exchange of information. There is also a need, he says, for further research into creating higher quality product and standardising machinery. “At the moment there is variation in quality and performance specifications such as calorific value, density, ash content, moisture content and size,” he observes.
Kevin Gikonyo, the social entrepreneurship leader at Hivos East Africa, an organisation that supports transitions towards renewable energy, says they implemented a briquette production programme in the Somali regional state of Ethiopia and have learnt valuable lessons.
The project uses the Jatropha plant (Jatropha curcas) and other invasive species in the region to make briquettes, and there are plans to introduce bamboo. “We have targeted refugees and host communities on a 50:50 grant share allocation in the Deka-suftu, Suftu and Dollo Ado areas,” Gikonyo says, adding that the project has included the technical skills transfer of entrepreneurship expertise, briquette production and the manufacturing of fuel-saving stoves and their parts.
The three-year project, supported by the Netherlands Enterprise Agency among other donors, ends in early 2021.
“The overall impact so far has been reduced environmental degradation, and fewer chores for women used to travelling distances to fetch firewood,” says Gikonyo.
While widespread use of the technology is still some way away, Venter’s optimism suggests a bright future for agro-waste as a source of clean energy in Africa.
“Maybe this is foolish to western trained business managers, but when it works, it works well. It is in a way, a real benefit to being on the front edge of the growth of a new process for combating climate instability,” Venter says. For BioAfriq Energy Limited it is about affordability, environment conservation and food security, while Veliz Foods is witness to a green promise.